The Future of Solar Energy in Manufacturing
- Noel Segui
- Mar 4, 2019
- 6 min read
The manufacturing economy is currently under-utilizing solar energy. But the long-term prospects for solar in this sector are excellent. In fact, manufacturing and solar could be a match made in heaven.
A handful of American manufacturers have already jumped on the solar bandwagon. Many more will likely join them soon. Solar energy in manufacturing is an ecological necessity and an economic winner.
Why Factory Owners Need Solar
Manufacturing facilities are hubs of activity. They use enormous amounts of energy in a wide variety of processes, all of which are scaled up for maximum intensity. The average factory in the United States consumes 95.1 kilowatt-hours of electricity per square foot annually, which is at least 10 times the amount of electricity used in the typical American home.
Heat makes up the bulk of a factory’s energy consumption. But electricity accounts for about 20 percent of the power used.
And this percentage us rising. Factories in the 1980s used 25-50 percent less electricity than they do now. By 2030, electricity may comprise as much as 30 percent of all manufacturing energy consumption.
The electrification of industry offers both challenges and opportunities. Challenges, because manufacturers that draw power exclusively from coal-burning power plants will contribute to the planet’s carbon dioxide-induced pollution problems. They will mean higher power bills, likely boosted by carbon taxes or other environmental penalties.
But renewable energy will offer opportunities to avoid these problems. Solar energy in particular could reduce the utility bills of manufacturers substantially.
Like many technologies, solar energy gains efficiency as its scale of deployment increases. In 2019, the average cost of installing a residential solar energy system was $3.05 per watt. But this price drops to only $1 per watt for systems with a one-megawatt generating capacity. This estimate comes from First Solar, the nation’s leading developer of commercial solar energy systems.
In comparison to coal, solar is a clear money-saver. Current solar technology is able to produce energy at half the cost of coal ($50 vs. $102 per megawatt-hour of power produced).
Solar Was Made for Manufacturing—and Vice Versa
Most manufacturing facilities are perfectly designed to meet the space requirements of solar. It’s almost as if architects and site planners were anticipating the eventual installation of solar panels.
Factories are generally constructed with square or rectangular roofs. This is an ideal design for rooftop solar arrays. Installers can work quickly and efficiently on these types of rooftops, cutting down on labor time.
Manufacturing plants are normally located far from tall buildings or trees that might block sunlight. Panels work at peak efficiency when oriented toward the southern sky, and that is easy to do on flat roofs without obstructions.
Ground-based solar arrays may be more suitable for some manufacturing facilities. This may be the case if rooftops are not flat, or if they are not capable of supporting excessive weight.
Fortunately, most manufacturing sites have the land area to accommodate ground-mounted systems. The land around factories often features large parking lots, or expansive greenfields and/or brownfields set far back from roads. These spaces are usually ideal for solar panel arrays, and if combined with rooftop panels, they can expand the size of a solar installation significantly.
When parking lots are the preferred location, solar canopies are an appealing option. These aesthetically pleasing structures can protect cars from the elements while simultaneously providing solar power.

Source: Flickr
Ground-based solar installations require approximately 100 square feet of land for each kilowatt of system capacity. Most factories will require a solar PV farm in the 100-kilowatt to one megawatt (1,000 kilowatt) range to offset a substantial percentage of their electricity needs. This translates into a quarter acre of land/space (10,000 square feet) for a smaller array and 2.5 acres (100,000 square feet) for a larger one.
These space requirements would not be prohibitive for most manufacturers. If roof space was inadequate or continuous plots of land were unavailable, smaller solar arrays could be mounted in multiple locations.
One drawback of solar energy is that it cannot supply power after dark. But this problem can be solved with the addition of a battery bank. Solar-compatible batteries can supply energy on demand, as long as some of the energy collected by solar panels goes unused during the day.
The Irresistible Economic Logic of Solar
Whatever the environmental benefits, manufacturers aren’t going to convert to solar energy unless it makes good economic sense.
Lending institutions do offer reasonable financing packages for solar energy installation. But even with a 10-percent commercial renewable energy tax credit, and any other rebates or tax advantages offered by states or localities, manufacturing-scale solar arrays will still be expensive. Likely in the $100,000 to $1 million range.
However, that initial sticker shock shouldn’t be a deal-breaker. Bids for large-scale solar installations are currently running at about 30 percent of the cost of a residential system. With minimal need for maintenance, solar energy is essentially free once an array is paid off. Over the 25-year lifespan of a typical solar energy system, inverter replacement will likely be the only significant maintenance or repair expense encountered.
For manufacturers unable or unwilling to invest in solar panels directly, Power Purchase Agreements (PPAs) could be an alternative. In fact, several prominent manufacturers have already chosen this option.
Solar installation and utility companies are often willing to enter into such agreements. They build or pay for solar farms or rooftop arrays built on factory owners’ property, while retaining ownership rights to the equipment. Manufacturers can purchase power the solar power produced at a set cost for a predetermined period of time, at a cheaper rate than would be available if buying through the grid.
Manufacturer Case Studies: General Motors, Crayola, Campbell Soup and Tesla
Some of the top manufacturers in the country have committed to solar energy. Toyota, L’Oréal, Johnson & Johnson, Nestle Purina, Anheuser-Busch, Owens Corning, Del Monte Foods, Mars Snackfood and Atlantic Coast Freezers are just some of the companies that have installed solar panels at their factories.
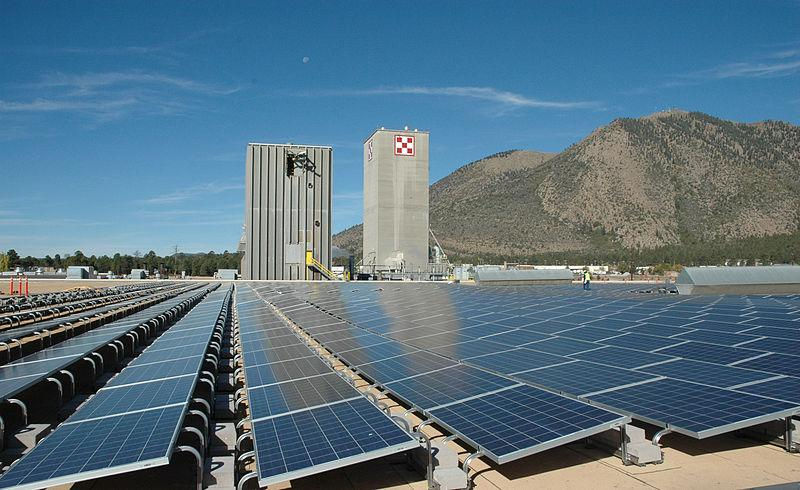
Source: Wikipedia Commons
Most of these manufacturers have installed smaller solar arrays with less than 100-kilowatt capacity. These systems allow them to defray at least some of their electricity costs, while limiting the size of their initial investments.
But there are companies that have made a more significant commitment to solar. Here are four that stand out:
General Motors
General Motors leads all U.S carmakers in solar panel deployment. The company has pledged to go 100-percent renewable by 2050, with solar and wind power sharing most of the load.
As explained by GM CEO Mary Berra:
“This pursuit of renewable energy benefits our customers and communities through cleaner air, while strengthening our business through lower and more stable energy costs.”
Overall, GM has installed 11 megawatts worth of solar panels at 16 U.S. manufacturing facilities. This includes a massive 850-kilowatt ground-mounted solar system at its Chevrolet Corvette plant in Bowling Green, Kentucky.
GM built its largest array to serve their transmission plant in Warren, Michigan. This ground-mounted system features a whopping 898 kilowatts of generating capacity. Unfortunately, that plant will close in 2019, and the ultimate fate of its solar panels is still unknown.
Crayola Crayons
In partnership with UGI Utilities and the renewable energy company PPL, Crayola Crayons built a 20-acre solar farm at its facilities in Forks Township in Pennsylvania. The farm includes more than 30,000 panels installed with a 2.4-megawatt generating capacity. It supplies enough power to manufacture one-third of the crayons and markers the company produces each year.
“Our solar project is one of many ways Crayola is incorporating social and environmental responsibility into our business to benefit our company, community and consumers.”
These were the words of Peter Ruggiero, a Crayola executive who spoke at the solar farm’s groundbreaking ceremony. Since its completion in 2010, Crayola’s solar project has been featured prominently in its marketing campaigns.
UGI and PPL provided the funds to build this solar facility. Crayola purchases electricity from these two under a PPA.
Campbell Soup
Campbell Soup has taken a deep plunge into solar energy. The company’s solar PV investments include a massive 9.8-megawatt array at its manufacturing plant in Napoleon, Ohio, and a 4.4-megawatt system at its world headquarters in Camden, New Jersey.
Campbell contracted SunPower to install its solar energy systems, which include ground-mounted and rooftop panels and solar canopies for its parking lots. SunPower owns all of the solar equipment, and Campbell purchases its output under a 20-year PPA.
Coming Attractions: The Tesla Gigafactory
No survey of solar energy in manufacturing would be complete without mentioning Tesla’s Gigafactory 1, which will produce many of the company’s electric vehicles and lithium-ion batteries.
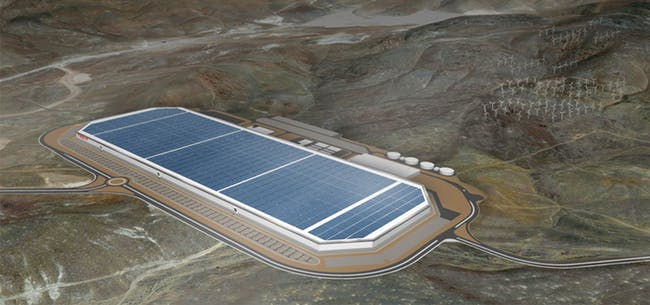
Source: Tesla
This mega-structure will cover 13 million square feet of space in the Nevada desert at completion, making it the largest building in the world. If all goes according to plan, much of its power will be supplied by a gargantuan 70-megawatt solar energy system installed on its rooftop.
Gigafactory 1 is up and running. But is still far from completion. Installation of solar panels on its rooftop only began in earnest in 2018.
Nevertheless, the company has not wavered from its plan to convert this factory to 100-percent renewable energy. According to Tesla founder Elon Musk, it will complete a full transition to renewables by the end of 2019.
Manufacturing Greater Profits with Solar Energy
Over the past several years, utility companies have been responsible for most of the growth in the U.S. solar energy market. In the first six months of 2018, utilities purchased a record-breaking 8.5 gigawatts of solar panel capacity. This happened despite President Trump’s implementation of a 30-percent tariff on panels imported from overseas.
Technological advance, plus promising economies of scale, have made large-scale solar energy projects more economically viable than ever before. What is happening with utilities can also happen in the manufacturing sector, and none of the manufacturers who’ve already installed solar panels have expressed any regrets about their decision.
Solar energy is the wave of the future, in manufacturing and everywhere else.
Cover Photo Source: Renewable Energy Partners, Inc.
Comments